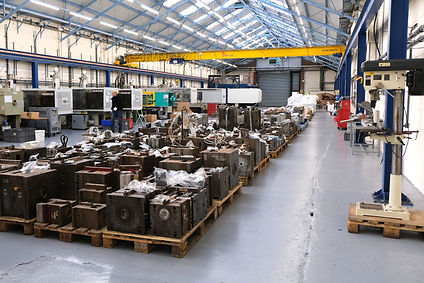
CASE STUDY
Injection Moulding
Client:
Hi-Tail
​
Location:
Hampshire, United Kingdom
​
Challenge:
Hi-Tail originally had the first prototype made in China, and the main body of the product was made from aluminium.
​
While aluminium did provide the necessary rigidity for the telescopic light to remain upright, it did mean production costs were high, and made the product heavier than was practical.
​
Following this, Hi-Tail began to consider plastic as an alternative material and after some computer modelling to calculate the proportions and dimensions needed, they asked Amey Plastics to produce a prototype.
​
Solution:
Following a set back with the initial prototype, Amey Plastics worked with Hi-Tail to amend the design and calculations to get the right thickness and dimensions.
​
During this process, Amey also helped turn a Perspex support section, designed to stiffen the telescopic light, and prevent it from twisting, into an in-built mud guard.
​
Outcome:
Using the new calculations and alterations from Amey, a revised prototype was produced that solved the rigidity issues.
​
Hi-Tail were very pleased with not just the quality of the revised prototype, but also the detailed and comprehensive advice offered by Amey Plastics, which ultimately helped solve design issues, and reduce the costs of manufacturing.
​
Hi-Tail will soon enter into the final field-testing phase, and will, following any feedback gathered, look to produce the final product.
​
If you have a project you’d like to discuss producing with us, or you have some technical queries, please do contact us on (+44) 01730 266525 or email sales@ameyplasticsltd.co.uk.